臭氧催化氧化技术在石化废水深度处理中的应用
石化污水处理厂二级出水可生化性低,含部分有毒难降解有机物。随着GB31571—2015《石油化学工业污染物排放标准》2015年7月1日的实施,我国石化污水处理厂迎来了一次集中处理技术升级,其大多采用以臭氧/臭氧催化氧化为核心的处理工艺建成深度处理单元,对石化污水处理厂二级出水进行深度处理使其达标排放。目前这类装置大多已运行超过2年,实际运行过程中,该技术出现了设计之初未曾考虑到的一系列问题,致使臭氧利用率不高且持续下降,治理成本逐年增高等。结合实际工程,从絮体、胶体大分子有机物、臭氧传质和催化剂4个方面对这些问题进行了系统分析,同时对臭氧催化氧化技术在石化污水处理厂二级出水处理中的发展方向进行了展望。
石化废水是石化工业在生产汽油、柴油、煤油、润滑油等石油产品以及乙烯、甲苯、合成树脂、合成橡胶和合成纤维等有机化工材料过程中产生的废水,同时还包括石化工业企业或生产设施区域内被污染的雨水、循环冷却排污水、锅炉排污水以及生活污水等。石化废水中含有苯系物、酯类、酚类、醛类、酮类、醇类、腈类、胺类、烷烃、多环芳烃、有机酸等多种有毒、难降解的有机物,属于典型的难降解工业废水。在经过不同程度的预处理后,石化废水通常再经综合污水处理厂统一处理,然后排放到受纳水体。我国石化综合污水处理厂原执行GB8978—1996《污水综合排放标准》,随着GB31571—2015《石油化学工业污染物排放标准》在2015年7月1日的实施[3],我国石化综合污水处理厂迎来了一次技术升级,大多数污水厂建成了以臭氧/臭氧催化氧化为核心的深度处理单元,实现了出水达标排放,有效降低了有毒和难降解有机物的排放。臭氧催化氧化对石化污水处理厂二级出水中难降解有机物的去除具有明显的效果,但是随着这类装置的长期运行,也存在若干问题需要总结、展望,其对完善该技术在石化废水深度处理中的应用具有重要的参考意义,也可为类似工程提供相关经验借鉴。
1、臭氧催化氧化技术在石化废水深度处理中的应用
高级氧化技术在高温、高压、电、声、光辐照、催化剂等反应条件下,产生具有强氧化能力的羟基自由基(·OH),·OH可以成功分解包括水中难降解有机物在内的大多数污染物,使大分子难降解有机物氧化成低毒或无毒的小分子物质。高级氧化技术包括臭氧催化氧化、光催化氧化、Fenton氧化等,其中臭氧催化氧化技术对废水中很多难降解有机物具有很好的去除效果,而且不会产生污泥等二次污染物,具有绿色、高的优点。目前国内50KG/h以上规模的大型臭氧发生器生产技术已经非常先进,甚至可以生产100KG/h以上规模的臭氧发生器,在国内招标中已经逐渐取代了进口大型臭氧发生器。大型臭氧发生器的臭氧功耗可以低于7KW·h/KG(以臭氧计,氧气源,25℃冷水条件下),臭氧浓度在6% ~14%间可调,功率因数不小于0.95。臭氧发生器生产技术和性能已达到国际先进水平。因此,以臭氧/臭氧催化氧化为核心的深度处理技术在石化废水深度处理工程得到广泛应用(表1)。从目前的应用效果来看,其出水水质较好,运行较为稳定;从发展趋势来看,今后必将在难降解工业废水处理中得到更多的推广和应用。
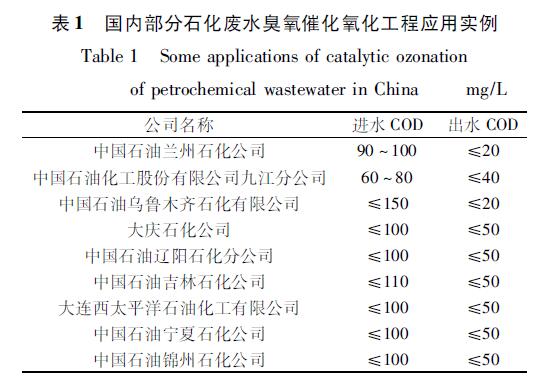
2、臭氧催化氧化深度处理石化废水存在的问题与分析
国内石化综合污水处理厂大规模进行深度处理提标改造在2015年左右,到目前为止建成的臭氧催化氧化深度处理装置运行大多已超过2年,该技术存在的一些问题也逐渐显现,主要表现在以下方面:
1)二沉池出水中絮体和大分子胶体有机物增加了臭氧单元的消耗和运行的稳定性;
2)臭氧催化氧化反应器(池)构型及运行模式不够优化,气液固三相传质效率不高;
3)催化剂通常不是针对石化废水生物处理出水水质设计,对于废水水质特异性不高,反应效率偏低。
2.1 絮体对臭氧催化氧化的影响
由于石化废水毒性较普通的城镇污水高,而有毒有机物对废水生物处理系统有不利影响,造成出水中悬浮物(SS,主要是有机絮体)浓度普遍比城镇污水处理厂出水中高,SS浓度一般高达25mG/L[4]。通常石化污水处理厂二级出水中SS和胶体物质占废水中有机物总量的15% ~20%,其主要成分为微生物残体,微生物分泌物〔如胞外聚合物(EPS)〕,溶解性微生物代谢产物(SMPS)以及所吸附的蛋白质、糖类等大分子有机物和重金属等无机物[5]。石化污水处理厂二级出水中絮体的存在会对臭氧催化氧化单元产生以下不利影响:
1)增加臭氧的消耗量。据研究,石化污水处理厂二级出水中SS超过75%为泥水分离不彻底随水流出的活性污泥细小碎片,其粒径为30~60μm,以有机质为主[6]。研究发现,采用臭氧催化氧化技术处理石化污水处理厂二级出水,单位化学需氧量(COD)的消耗量会随废水中SS浓度的增加而增加,这是因为废水中的生物絮体可以与臭氧发生反应,增加了臭氧消耗和投加量,从而影响废水臭氧催化氧化的效率,增加了该技术的应用成本[4]ZucKEr等[2]的研究表明,即使在反应刚开始的1S内,臭氧也显示出与颗粒物反应的倾向,臭氧与水体中颗粒物的反应速度很快。王雅宁[7]采用臭氧催化氧化技术处理石化污水处理厂二级出水,结果发现,当进水SS浓度为0~10mG/L时,去除单位COD平均消耗臭氧量为1.17G/G;当进水SS浓度升到30~35mG/L时,去除单位COD平均消耗臭氧量升至2.31G/G。张斯宇等[5]研究发现,当臭氧投加量低于10mG/L时,臭氧基本与石化污水处理厂二级出水中絮体不发生反应;当其投加量高于10mG/L时,臭氧可与絮体快速反应,遵循溶解性有机物、外层疏松型EPS和内层紧密型EPS的顺序。
2)絮体覆盖在催化剂表面妨碍了臭氧和溶解性有机物向催化剂表面的传质,从而降低反应效率。研究表明,臭氧催化氧化可以影响废水中絮体颗粒大小的分布,可以增加絮体的凝聚作用,使颗粒发生聚集,形成尺寸更大的絮体[2],从而在催化剂床层被截留。在实际生产中发现,若不对石化污水处理厂二级出水中的SS加以控制,直接采用臭氧催化氧化时,处理效果在7h内就会显著下降,而反洗可有效提高处理效率,但频繁反洗会增加催化剂间的摩擦和剪切,造成催化剂活性成分的流失,降低了催化剂的使用寿命,无形中也提高了该技术的应用成本。
3)对石化污水处理厂二级出水中特征有机物的去除产生不利影响。zhang等[8]采用臭氧催化氧化技术处理石化污水处理厂二级出水,研究发现,其可有效去除出水中的酯、醇、烯烃、酮和含氮类有机物,去除了进水中检出12种主要特征有机污染物中的6种,石化污水处理厂二级出水经0.45μm膜过滤后再进行催化氧化,出水中目标特征污染物可减少至3种。GB31571—2015对60种(类)特征有机物的排放浓度有明确的限定,因此去除石化污水处理厂二级出水中的SS,对特征有机物的去除也有一定的促进作用。
近年来,关于生物絮体的研究多聚焦于生化处理系统[9]。针对絮体对臭氧催化氧化等深度处理技术的影响还缺乏系统深入的研究,这在很大程度上限制了对石化废水总体处理成本的认识,进而影响高效生物处理技术在废水处理工程中的应用与发展。而对于二级出水后进入深度处理阶段的生物絮体研究更是十分有限。为此,需加强生物絮体在深度处理前后的对比研究,系统深入地研究生物絮体对臭氧催化氧化等深度处理技术的影响,研发针对石化污水处理厂二级出水水质的高效絮体去除技术,是下阶段石化污水处理厂二级出水深度处理技术研发的重点。
2.2 胶体大分子有机物的影响
由于胶体物质颗粒小、质量轻、单位体积的表面积大等特点,其表面能吸附大量的离子并带负电,使得胶体之间相互排斥而处于稳定状态。水中的胶体大分子物质不能凭借自身重力沉降,需在水中加入药剂来破坏其稳定性,使胶体脱稳、增大以沉降去除[10、11]研究表明,胶体类有机物占石化污水处理厂二级出水中COD的9% ~15%[12],这类物质由于分子量较大,臭氧催化氧化也不能有效将其去除,但其会影响臭氧催化氧化单元的处理效率。向石化污水处理厂二级出水中投加25mG/L聚合氯化铝(PAC)混凝剂去除其中的胶体类有机物后再进行臭氧催化氧化,与直接对石化污水处理厂二级出水进行臭氧催化氧化相比,同等条件下COD的去除率可提高11%左右,这是由于石化污水处理厂二级出水中胶体大分子有机物的存在影响初始阶段(t<30S)臭氧催化分解的速率,从而减少了·OH的产生量[13]研究表明,预处理臭氧投加量为1mG/mG〔以总有机碳(TOC)计〕时,对溶解性有机碳(DOC)的去除效果改善不太显著[14]Jin等[15]研究了一种新型的臭氧混凝工艺,并探讨了不同PH下混凝、复合型臭氧氧化混凝(hybrid ozonation-coagulation (HOC)、预臭氧混凝对DOC的去除率,结果表明,该工艺比传统的臭氧混凝技术对有机物的去除效果更为显著。研究表明,在污水深度处理过程中,胶体类大分子有机物主要影响臭氧催化氧化过程中特征有机物的去除[8]。由于GB31571—2015中限定的特征污染物种类较多,排放限值较严格,在进入臭氧催化氧化单元之前进行有效的预处理显得十分必要。但目前缺少石化污水处理厂二级出水中胶体大分子有机物对特征污染物去除影响的相关报道,石化污水处理厂二级出水中胶体大分子有机物的存在对臭氧催化氧化深度处理的影响也是未来该领域的研究重点。
2.3 臭氧传质的影响
臭氧氧化水中有机污染物依靠臭氧从气相传至液相,扩散后与目标污染物进行反应,臭氧向液相中的传质效率直接影响臭氧氧化的效果[16]。臭氧总传质系数主要取决于气液两相紊流程度、臭氧气泡尺度和数量、两相接触传质相界面积以及臭氧氧化反应动力学等诸多因素。过程速率通常受臭氧从气相传质进入液相过程的限制[17]。在相同气体流量下,气泡尺寸越小,则相界面积越大。增加气液两相传质相界面积,不仅有利于提高过程的总传质速率,也有利于提高臭氧的利用率[18]REn等[19]采用微孔反应器模型进行研究,发现微孔反应器的使用可显著提高传质效率和污染物的去除效果。张勇等[20]采用疏水膜膜接触反应器(其气液接触界面是膜的表面)研究臭氧传质规律及其对模拟印染废水的降解规律,发现膜接触反应器可有效提高臭氧氧化速率以及臭氧利用率。臭氧和水的混合方式经过多年改进和研究,目前主要有鼓泡法和射流法,传质效率不断提高。但实际应用中,臭氧催化氧化多采用气液逆向流的构筑物形式,即臭氧从底部曝气,石化污水处理厂二级出水从催化氧化池顶部进入,催化氧化后的出水从池体底部流出,逆向流的方式可增加臭氧的传质效果。臭氧向液相中转移的速率较快,在水中的溶解度是氧气的10倍以上[21]。通常限制石化污水处理厂二级出水处理效果的是有机物的氧化速率,从化学反应的角度来讲,气液同向流可保证很大污染物浓度、催化剂投加量、很高臭氧浓度同时存在的条件,有机物氧化的速率很快[22]。目前的研究多局限于小试装置,还缺少生产规模的试验验证。研发适合石化污水处理厂二级出水水质的臭氧催化氧化反应器,探讨很佳运行模式,提高气液固三相的传质效率,成为提高臭氧催化氧化效率的研究重点,对石化污水处理厂节能降耗意义重大。
2.4 催化剂对处理效果的影响
臭氧催化氧化通常是在催化剂的辅助作用下,促进臭氧分解产生更多的·OH,利用·OH分解水中的有机污染物。·OH的氧化还原电位较高,为2.8EV,·OH具有很高的氧化活性,几乎可与所有的有机物(包括芳香族化合物、脂肪族化合物和油脂等)发生反应,生成小分子物质或者直接矿化[23、24]。催化剂是提高臭氧催化氧化效果的关键。高效复合型臭氧催化剂属于非均相催化氧化,其利用金属氧化物及其固态金属达到臭氧催化氧化水中有机物的目的[25]。由于这种催化剂具有成本很低,容易推广以及制备、回收,重复使用率高等优势,在石化污水处理厂二级出水臭氧催化氧化中广泛采用。为了提高催化剂的催化效率,通常将其负载在比表面积较大的载体上[26]。催化剂投加量和催化剂比表面积的增加,使得吸附在催化剂表面的臭氧发生转化并生成具有强氧化性的·OH,·OH可以在催化剂表面和溶液中发生自由基链式反应,从而提高臭氧利用率,进而提高水中有机物的去除率[27]。
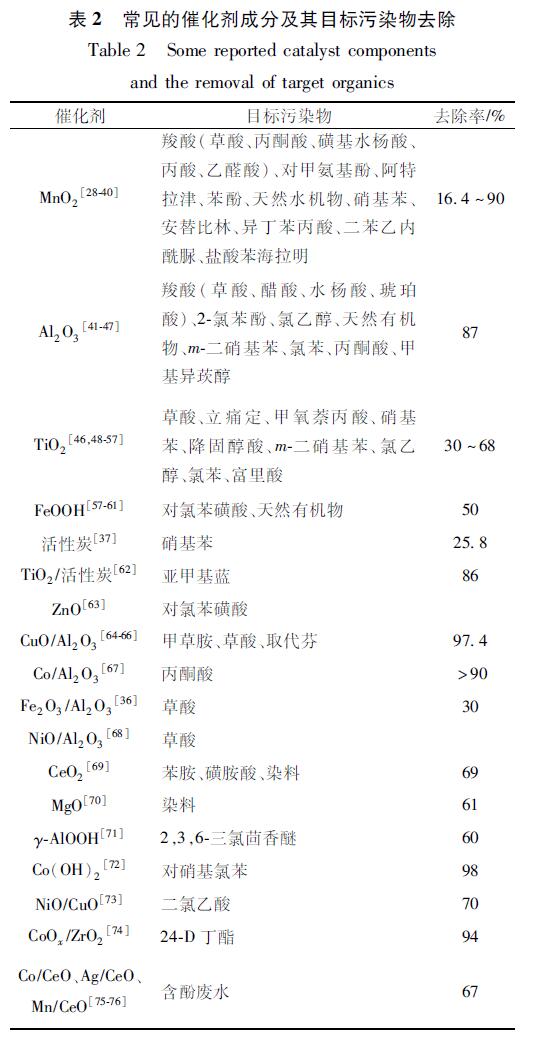
实际工程中,臭氧催化氧化对石化污水处理厂二级出水COD的去除率一般低于45%。为提高该单元COD去除率,催化剂的填充率一般高于50%,臭氧的投加量也普遍高于30mG/L。如前文所述,较高的催化剂填充率使得该单元具有显著的絮体截留作用,会进一步增加臭氧投加量,降低处理效率,导致反洗频繁,而频繁的反洗会增加催化剂间的摩擦和活性成分的流失。因此,研发针对石化污水处理厂二级出水水质的高效催化剂,是未来该领域的发展趋势。
目前在臭氧催化剂研发方面开展了大量的研究,主要研究思路是采用目标污染物配水进行相关高效催化剂研发(表2)。研发的催化剂在理论上具有对目标污染物较好的去除效果,但在水质复杂的实际废水中应用是否能维持较高的处理效率目前并不明确,且部分催化剂采用贵重金属氧化物研制,成本较高,不适于实际工程应用。
目前市场上针对石化污水处理厂二级出水水质的高效催化剂核心技术仍掌握在国外一些著名环保公司手中,为此亟需进行针对石化污水处理厂二级出水水质的专属高效臭氧催化剂的研究。高效的催化剂可降低实际应用的填充率,减少絮体截留,降低反洗频率,对整体降低石化污水处理厂二级出水臭氧催化氧化单元处理能耗方面起着举足轻重的作用。
3、结论与展望
(1)混凝预处理技术可以去除废水中悬浮物和胶体物质,未来应探索更适合石化污水处理厂二级出水臭氧催化氧化技术的混凝预处理技术及参数,提高混凝预处理工艺的运行效率,使之与臭氧催化氧化技术相耦合。
(2)臭氧气液固传质是一个较为复杂的过程,通过增加气液固三相传质相界面积,探讨微孔分布器对总传质速率的影响及应用效果,结合计算流体力学(CFD)和催化动力学,强化传质过程,研发适合石化污水处理厂二级出水的臭氧催化氧化反应器,探讨其很佳运行模式,提高气液固三相的传质效率,从而提高臭氧利用率。
(3)臭氧催化剂是臭氧催化氧化的核心,需要有针对性地研发适合石化污水处理厂二级出水水质的低成本、易制备和回收、重复使用率高的专属高效复合型催化剂。
来源:李亚男,谭煜,吴昌永,等.臭氧催化氧化在石化废水深度处理应用中的若干问题[J].环境工程技术学报,2019,9(3):275 281