臭氧能降解印制电路板(PCB)产生的有机废液吗
印制电路板行业在生产印制电路板 (PCB)过程中涉及大量有机溶剂、醚类有机物以及表面活性剂等,产生的废液中包含的有机污染物组成复杂、浓度高、毒性大且难以降解。目前,企业针对高浓度难降解 PCB有机废液的处理方法主要是 Fenton氧化法,但该方法存在有机物降解不彻底、Fenton试剂不能循环利用且处理费用高等问题。因此,急需寻找高效、安全且低成本的处理技术来对该类废液进行治理。
高级氧化工艺 (AOP)主要包括 Fenton/photo-Fenton、湿法氧化、光催化氧化以及臭氧氧化等技术。其中,催化臭氧氧化技术克服了臭氧氧化法中存在的不足,能在常温常压下高效降解大部分有机污染物且无二次污染,从而备受关注。大部分研究表明,催化剂的加入会促进活性自由基的产生。其中,羟基自由基 ( · OH)是催化臭氧氧化过程的主要活性自由基,对有机物的降解起关键性作用。目前,使用较为广泛的是非均相催化剂,主要包括金属和金属氧化物负载、金属氧化物,活性炭以及其他多孔材料等。金属氧化物催化剂(如MnO2、MgO、ZnO、TiO2、Al2O3和 CeO2等)、金属氧化物载体的材料 (如 Al2O3、TiO2等)、多孔材料载体(如石墨烯、碳纳米管等)都已经用于催化臭氧氧化过程,并且已经被证明具有良好的催化活性。然而,很多催化剂在制备及应用时存在一些缺点,如制备工艺复杂、成本较高、重复利用率低等,这些因素限制了催化臭氧氧化技术在实际高浓度难降解工业废液的应用。在催化臭氧化过程中,氧化钙(CaO)很少用于催化臭氧化过程;但初步实验表明,CaO结合臭氧氧化法,在处理实际工业废液中有机污染物时具有很大的优势,并且 CaO具有活性高、成本低、毒性低、pH稳定性好和环境友好的特点,因此,将其应用于催化臭氧氧化过程有良好的发展前景。
本研究探讨了 PCB废液降解过程中的催化降解机理以及有机物降解途径,考察了催化剂的循环稳定性并分析催化剂失活的可能原因;通过单纯形优化实验考察了 CaO在 PCB废液的臭氧氧化过程中的催化性能,包括 CaO质量、pH、臭氧浓度、降解时间和废液深度对废液中有机物降解率的影响;很后,将 CaO 催化臭氧过程应用于实际高浓度难降解废水并探讨其应用潜能,为实际工业废水的处理提供参考。
1、 PCB废液处理应用
1.1 单纯形优化实验
有研究表明,pH变化对催化效率有很大影响,这可能会影响催化剂的表面性质和活性自由基的产生。废液深度的变化会影响 O3分子与废液的接触时间,从而影响废液的降解率。O3在催化臭氧氧化过程起氧化作用。臭氧用量的增加,可以促进活性自由基的产生并且可以增加臭氧与废液的接触面积,从而促进废液中有机物的降解。因此,废液 pH、CaO质量 (m)、废液深度(h)、降解时间 (t)、臭氧用量等工艺条件的优化就显得尤为重要。考虑到 CaO会造成固废以及时间成本,因此,综合考虑了 CaO质量、降解时间和 COD 去除率 (η)三者的关系,以 0.7η+0.1/t+0.2/m为考察指标进行单纯形优化实验。表 4显示各因素的初点和步长,即各个因素的初始值以及变化值。表 5为根据均匀设计表 U6(65)得到的初始实验条件,经过优化之后得到的优化结果如表 6所示。可以看出,pH 为 12.6~13.2,降解时间为 150~180 min以及臭氧量为 120 ~200 mg·min−1时会取得较好的催化降解率。综合考虑固废以及时间成本,pH为12.97、CaO质量为1.0 g、废液深度为11 cm、降解时间为 150 min、臭氧用量为 120 mg·min−1时,COD去除率可达到 90.045%,并且 0.7η+0.1/t+ 0.2/m综合效率为 0.870 3,能够满足在较短时间、较少催化剂用量下取得较高的降解率,可以应用于高浓度难降解有机废水的处理。
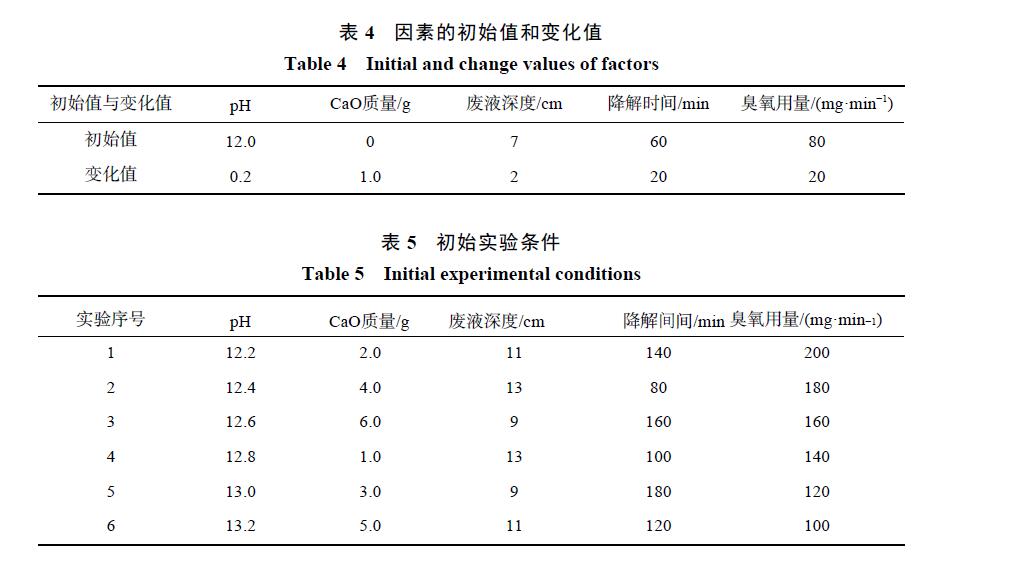
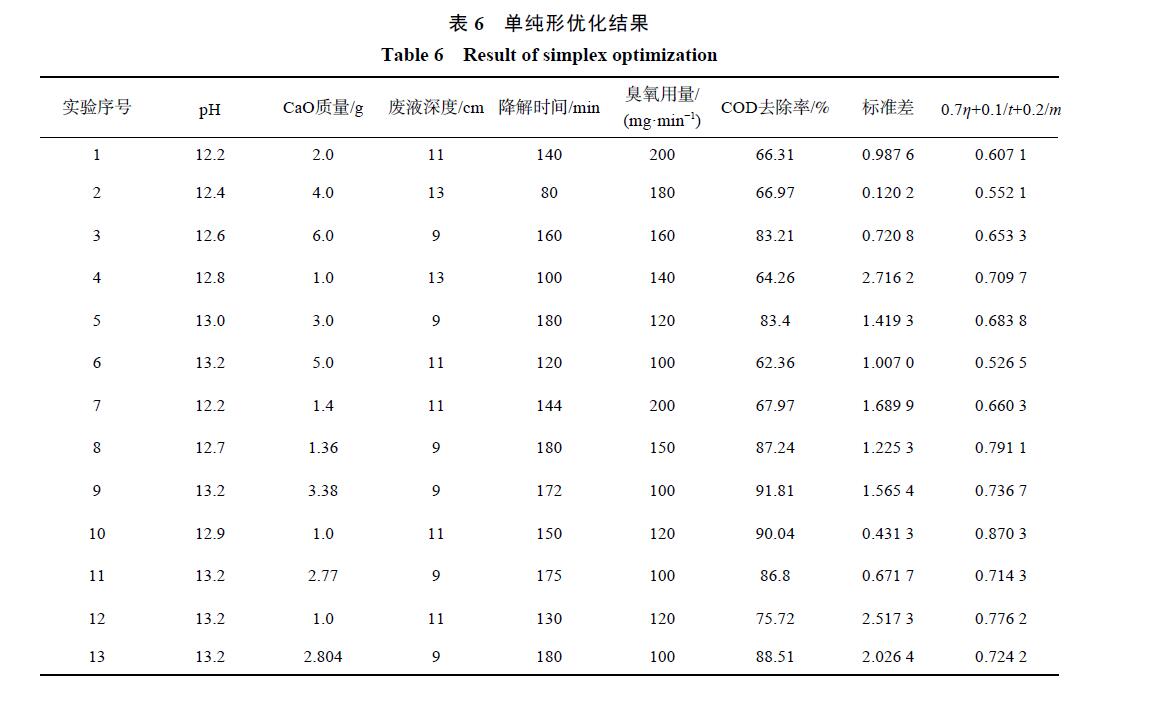
1.2 实际PCB废液处理效果
图 11显示了 CaO催化臭氧氧化处理工厂的实际 PCB清槽剂废液的处理效果,其工艺条件如下:pH为 13.0、CaO质量为 2.0 g、废液深度为 11 cm、降解时间为 180 min、臭氧用量为 180 mg·min−1。可以看出,处理 180 min后,废液 COD去除率达到了 94.67%,比单独臭氧氧化过程 COD去除率高 26.92%,CaO作为催化剂加入到臭氧氧化过程大幅度提高了有机物的降解率。上述结果表明 CaO催化臭氧氧化处理实际高浓度难降解废液具有可行性,并且对有机物的降解效果显著,具有广阔的应用前景。
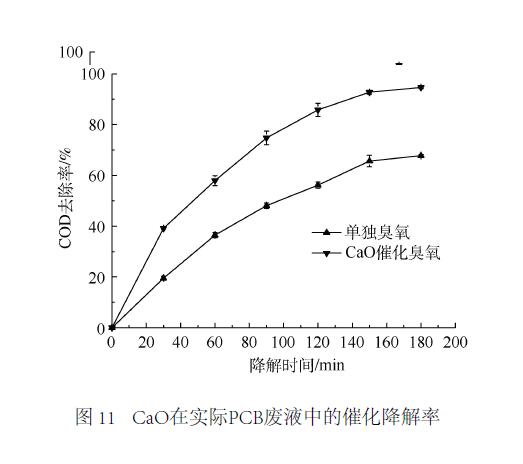
2、结论
1) 自由基淬灭实验和水杨酸羟基化实验结果表明,CaO 催化臭氧氧化体系中存在 · OH,主要是遵循羟基自由基机理。
2) 通过GCMS 检测,废液降解后检测出了中间体,如羟基丙酮、乙二醇、正丁醇、乙酸等。因此,有机物可能降解途径是:有机物主要是先与 · OH 结合,再进一步被氧化形成酮,然后被氧化为乙酸,很后形成CO2 和H2O。
3) 催化剂稳定性测试表明,CaO 具有优良的循环稳定性,经过5 次循环后,催化剂的催化效率可以达到84.04%。SEM、XRD 测试结果表明,使用后的催化剂团聚现象明显增大,其主要成分由CaO 变为了Ca(OH)2 和CaCO3,从而导致催化效率降低。
4) 单纯形优化实验表明,在优化条件下可以满足在较短时间,使用较少催化剂情况下,催化效率达到90.04%。很后,将CaO 催化臭氧氧化技术应用到实际PCB 废液中,废液COD 去除率可以达到94.67%,表明CaO 催化臭氧氧化技术可应用于实际高浓度难降解废液。
鲁蓝锶,陈际达*,鄢婷,付登林,文亚男,邓智博,张柔
重庆大学化学化工学院,重庆 401331
第一作者:鲁蓝锶(1994—),女,硕士研究生。研究方向:催化臭氧氧化技术。